Research Journal of Applied Sciences, Engineering and Technology
Pull-out Resistance Parallel to Grain of Threaded Steel Rod Glued-in Glubam with Edge Distance Variation
Research Journal of Applied Sciences, Engineering and Technology 2020 17: 1-6
Cite This ArticleAbstract
This study aimed to obtain the pull-out resistance parallel to the grain of the threaded steel rod glued-in glubam with various edge distances. The wood structures, both for connection and for reinforcement, used glued-in rods connection. However, there was no research on the application of glued-in-rod into the connection of structural elements from glued laminated bamboo (glubam) due to lack of information on the basic characteristics of the glued-in rod on laminated bamboo. This experiment tested the pull-out resistance and stiffness of the threaded steel rod bounded parallel to the grain in laminated bamboo with varying edge distances. The dimension of laminated bamboo specimens were100×100×100 mm, the threaded steel rod diameter was 10 mm, the drill hole diameter was 14 mm and this research used sikadur 732 as the adhesive. This experiment made eight various edge distances: 1d; 1.5d; 2d; 2.5d; 3d; 3.5d; 4d; and 4.5d, with d as the threaded steel rod diameter and made five replicas of each variation. The results showed that the 3d edge distance or greater had the constant pull-out resistance while less than 3d edge distance had less pull-out resistance. The slip modulus for the threaded steel rod glued-in glubam in this study was not influenced by edge distance with a range 3.732 kN/mm to 7.768 kN/mm.
Keywords:
Introduction
There are numerous researches on glued laminated bamboo (glubam) application for construction. The researches included beam and column structural elements (Xiao et al., 2010; Sinha et al., 2014; Karyadi and Susanto 2017; Karyadi et al., 2018).
Assembling structural elements into building structures require a connection using various shapes and materials. Recently, there was a development of a glued-in rod connector and its application in wood structure; both for connector (Gonzalez et al., 2016; O'Neill et al., 2017; Gattesco et al., 2010) or reinforcement (Steiger et al., 2015; Harte et al., 2015).
However, there was no study in glued-in rod applications on the connection of laminated bamboo structural element. The reason were due to the lack of information on the base characteristic of glued-in rod in laminated bamboo. Research by Yan et al., (2016) offered information about the effect of the depth and diameter of the glued-in rod on the pull-out strength. Nonetheless, it left many unresearched parameters. Therefore, this research aimed to study the distance effect between the threaded steel rod and the edge of laminated bamboo on the threaded steel rod pull-out resistance, slip modulus and types of failure.
Researchers have developed formulas to calculate the pull-out resistance of glued-in rod application in wood material. The formula developed by Steiger et al., (2006), Yeboah et al., (2013) and Yan et al., (2016) is usefull to calculate the glued-in rod pull-out resistance with edge distance greater than or equal to the allowed minimum distance. Generally, Stepinac et al., (2013) concluded that there are three main parameters involved in the above formula, e.g., the diameter of the glued-in rod, glued-in length and interfacial layer shear strength between wood and glue or between glue and rod. Similar to the conclusion above, Stepinac et al., (2013) and Yan et al., (2016) formulated the Eq. (1):
$ \text F=L_{a}\times \pi \times d_{a} \times f_{v} $
with,
F : Glued-in rod pull-out resistance
La: Glued-in length
da : Diameter of the rod
fv : Interfacial shear strength
$ \pi $ : Mathematical constant
Deng (1997) and New Zealand Timber Design Guide (NZW 14085 SC, 2007) developed another formula that including the distance between the glued-in rod and the edge of the timber displayed in the Eq. (2):
$ \text Q_{k}=Cd.k_{b}.k_{e}.k_{m}(l/d)^{0.86}.(d/20)^{1.62}.(h/d)^{0.5}.(e/d)^{0.5} $
Within the Eq. (2); $ Q_k $: pul-out resistance (N), (kN), $ k_b$, $k_e$, $k_m$: bar type factor, epoxy factor, moisture factor respectively,l: glued-in length (mm), d: diameter of steel rod (mm),h: diameter of the drill hole (mm), e: edge distance (mm),Cd = 8.54 for Deng (1997) formula and Cd = 6.73 for New Zealand Timber Design Guide (NZW 14085 SC 2007).
The amount of slip during pull-out resistance were also crucial to note.This parameter is vital to determine the connection rigidity using the glued-in rod as stated in the slip modulus ($K_s$),calculated with the formula of (BS EN 26891, 1991):
$K_{s}=\frac{0.4F_{max}}{4/3\left(d_{04}-d_{01}\right)}$
with,
$K_s$: Slip modulus (kN/mm)
$F_max$: Maximum load (kN)
$d_{04}$ : Slip at 40% $F_{max}.(mm)$
$$ d_{01}: Slip at 10% $F_{max}.(mm)$
Materials And Methods
This research obtained 3-5 years old Asian bamboo (Dendrocalamus asper Backer) Malang, East Java, Indonesia. Then, cut and split them into 5×20 mm in cross-section and 1 m in length strips. Soaked the bamboo strips in a mixture solution of 1% boric acid ($H_{3}BO_{3}$) and 1% borax ($Na_{2}B_{4}O_{2}$) and dried. Glued the strips with less than 12% moisture content into each other using $268 g/m^2$ urea-formaldehyde adhesive and cool-pressed in 2 MPa for four hours (Karyadi and Susanto 2017). After, reaped the materials. Cut the laminated bamboo into 100 mm×100 mm×100 mm dimensions and drilled 14 mm diameter and 40 mm depth. The varying distances between the drill holes of the laminated bamboo edge were 1d, 1.5d, 2d, 2.5d, 3d, 3.5d, 4d, 4.5d; where d was the diameter of threaded steel rod with five replicas for each variation. The threaded steel rod with $f_{y} = 350 MPa$ in 10 mm diameter and 250 mm length then put into drill holes. Before, gave the adhesive epoxy type in sikadur 732 brand (Fig. 1) in the drill hole.
This research used the Universal Testing Machine (UTM) with 1000 kN capacity and 0.1 kN precision to test the pull-out resistance and the dial gauge with 10 mm capacity and 0.01 mm precision to find the amount of the slip during the test. Figure 2 displays the test set up using loading configuration pull-compression.
This study used the Eq. (4) and (5) to calculate the amount of slip:
$ \Delta S = Y-\Delta L $
Calculating ΔL used the formula:
$ \Delta L=\frac{PL_o}{\Delta S.E} $
In Eq. (4) and (5),
Δs : Slip
Y : Increased total length
E : Modulus of elasticity of threaded steel rod
ΔL : Increased length of threaded steel rod
P : Load
$A_s$: Cross-sectional area of threaded steel rod
$L_o$: Initial threaded steel rod length
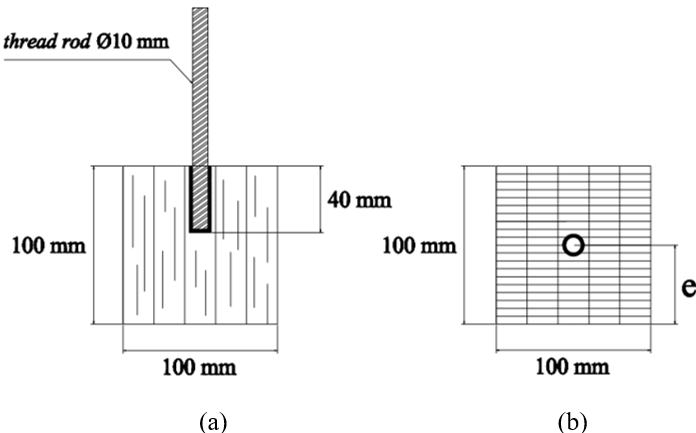
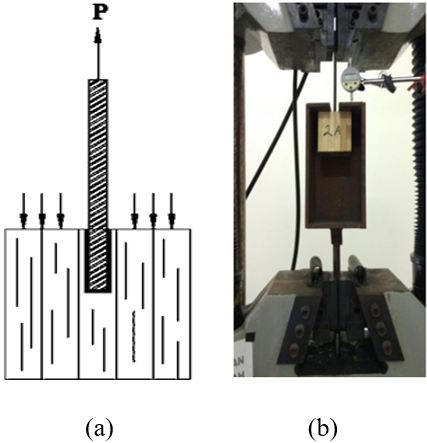
Results And Discussion
The moisture content on laminated bamboo right after the test was 15.56% based on ASTM (2003). The Specific Gravity test from laminated bamboo referred to the ASTM (2014) with the result of $0.687 g/cm^3$ that was similar to the research of Malanit et al., (2011) with the result of $0.720 g/cm^3$. The pull-out resistance test results from threaded steel rod with the varying edge distances of 1d, 1.5d, 2d, 2.5d, 3d, 3.5d, 4d, 4.5d obtained the pull-out resistance, the damage types that occurred and slip modulus as explained below.
Threaded steel rod pull-out resistance: Threaded steel rod pull-out resistance: In this research, the pull-out resistance results indicated that the minimum distance of threaded steel rod before decreasing the pull-out strength occurred at 3d edge distance with the value of 19.72 kN and the shear strength, calculated using Eq. (1), was 11.209 MPa. The similar shear strength value was obtained by Yan et al., (2016), with the result of about 10.54 MPa. Table 1 lists the complete results of the pull-out resistance test for all varying edge distance.
At the 2.5d edge distance, pull-out resistance and shear strength declined to 17.40 kN and 9.890 MPa. The value drops for 11.76% from 3d edge distance. At a 2d edge distance or less, the pull-out resistance kept declining as observed from Fig. 3.
The drop in pull-out resistance is caused by the splitting failure that occurred in the specimens before the maximum load in the glued-in rod was achieved. Therefore, the load value is lower compared to the specimen with no splitting failure. Figure 3 shows the correlations between edge distance and pull-out resistance results from the test. Whereas Fig. 4 shows the comparison in pull-out resistance between glued-in rod in laminated bamboo with equation approach of the glued-in rod in wood.
Figure 4 indicates that this research results in pull-out resistance were similar to the pull-out resistance calculated using the equation of Deng (1997) and higher than the pull-out resistance calculated using the equation of New Zealand Timber Design Guide (NZW 14085 SC 2007), or Eq. (2). The dissimilarities were the results of material differentiation. This research used laminated bamboo material while Deng (1997) and New Zealand Timber Design Guide (NZW 14085 SC 2007) used the wood material. Although varied in pull-out resistance, the trendline that occurred shows an almost similar pattern. The similarity shows that increasing edge distances caused an increase in pull-out resistance. Blass and Laskewitz (1999) stated that the minimum steel rod edge distance in wood specimen before pull-out resistance and shear strength declined was at 2.5d; while Steiger et al., (2006) gave 2.3d distance.
Types of failure in glued-in rod connection: Based on Table 2, samples with the edge distance less than twice the diameter of the threaded rod experienced splitting failure in the laminated bamboo (Fig. 5b). Samples with the edge distance more than or equal to twice the diameter of the threaded rod experienced damaged, such as pulled threaded rod along with bamboo surfaces around the epoxy adhesive (Fig. 5a). From the damage type that occurred, in summary, the minimum threaded rod distance from the outer edge of laminated bamboo to prevent the splitting failure in laminated bamboo was at twice the diameter from the outer edge laminated bamboo.
Research on pull-out resistance in the glued-in rod of wood by Gattesco et al., (2010) stated that splitting failure is the most frequent damage among others. Preventing this problem requires knowledge on the minimum distance between the steel rod to the specimen’s edge. Results from Gattesco et al., (2010) showed that the minimum distance required was 2.3 times the diameter of the steel rod to prevent splitting failure on wood. In this research, the minimum distance required was at 2d towards laminated bamboo.
Slip modulus: Pull-out resistance in glued-in rod resulted in a curve between loads (P) and slip (ΔS) as observed in Fig. 6. Two important things from this figure are the slip modulus and the collapse model.
The almost similar slope shows that the edge distance did not influence the slip modulus from the glued-in rod in this research. In Table 3, the average values of slip modulus calculated by Eq. (3) is between 3.732 kN/mm to 7.768 kN/mm. Maria and Ianakiev (2015) found that the slip modulus was 1.18 kN/mm for a glued-in rod in 60 mm anchored length in Douglas Fir Wood. Verdet et al., (2016) tested glued-in rod with epoxy adhesive (Sikadur 330, Sika, Le Bourger, Switzerland) and timber glulam produced from Black Spruce at 20°C temperature resulted in slip modulus of 108 kN/mm. Rossignon and Espion (2008) tested glued-in rod in glulam 160 mm anchored length in Norway Spruce with epoxy adhesive and obtained the initial modulus of 94.6 kN/mm. The main parameter that caused the varieties in the slip modulus from this research and the other mentioned research above was the embedment length, the material and the adhesive that was used.
In this research, the sudden drop of glued-in rod ability to resist the loads identified the brittle failure, as seen in Fig. 6. This type of collapse occurred due to interfacial damage between glue and bamboo that eliminate interfacial shear strength. Gonzalez et al., (2016) discovered that glued-in rod with embedment length 7.5 times the diameter of rod experienced a brittle failure, while rod with 10 times diameter embedment experienced a ductile failure. Maria and Ianakiev (2015) found that brittle failure occurred in pull-out resistance of 8 mm diameter glued-in rod in an Oak Timber and Douglas Fir Timber with embedment length 60 mm.
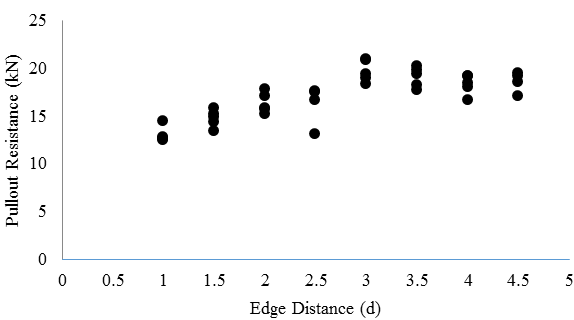
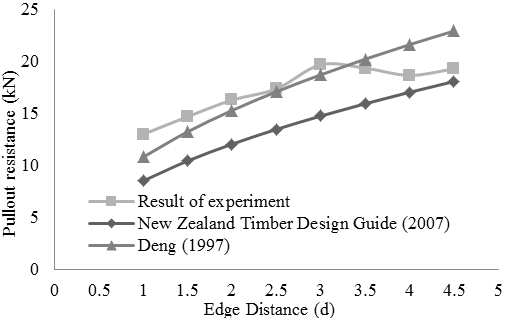
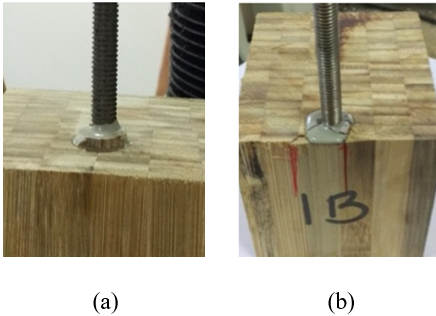
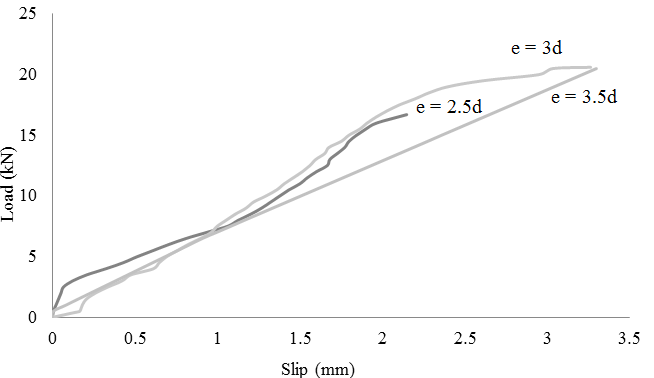
Specimen code | Edge distance (e) (mm) | Diameter of treaded rod (d) (mm) | Anchored length (Lo) (mm) | Bounded area (As) (mm2) |
---|---|---|---|---|
S1-d | 10 | 10 | 40 | 1759 |
S1.5-d | 15 | 10 | 40 | 1759 |
S2-d | 20 | 10 | 40 | 1759 |
S2.5-d | 25 | 10 | 40 | 1759 |
S3-d | 30 | 10 | 40 | 1759 |
S3.5-d | 35 | 10 | 40 | 1759 |
S4-d | 40 | 10 | 40 | 1759 |
S4.5-d | 45 | 10 | 40 | 1759 |
Specimen code | Number of specimen | Average of Pull-outresistance (P) kN | Standard deviation kN | Average of shear strength (fv) MPa |
S1-d | 5 | 13.020 | 0.835 | 7.401 |
S1.5-d | 5 | 14.720 | 0.915 | 8.367 |
S2-d | 5 | 16.320 | 1.085 | 9.276 |
S2.5-d | 4 | 17.400 | 0.483 | 9.890 |
S3-d | 5 | 19.720 | 1.190 | 11.209 |
S3.5-d | 4 | 19.400 | 0.864 | 11.027 |
S4-d | 4 | 18.700 | 0.600 | 10.629 |
S4.5-d | 4 | 19.325 | 0.665 | 10.985 |
Specimen code | Diameter of treaded rod (mm) | Edge distance (d) | Number of specimen | Types of failure | ||
---|---|---|---|---|---|---|
Pulled | Splitting | |||||
S1-d | 10 | 1 | 5 | - | 5 | |
S1.5-d | 10 | 1.5 | 5 | 1 | 4 | |
S2-d | 10 | 2 | 5 | 5 | - | |
S2.5-d | 10 | 2.5 | 5 | 5 | - | |
S3-d | 10 | 3 | 5 | 5 | - | |
S3.5-d | 10 | 3.5 | 5 | 5 | - | |
S4-d | 10 | 4 | 5 | 5 | - | |
S4.5-d | 10 | 4.5 | 5 | 5 | - |
Edge distance(e) (mm) | Threaded rod diameter(d) (mm) | Anchored length(mm) | Initial length(Lo) (mm) | Maximum pull-out load(P) kN | Slip at max. pull-out load (ΔS) (mm) | Slip modulus(Ks) kN/mm |
---|---|---|---|---|---|---|
10 | 10 | 40 | 153.0 | 13.020 | 2.251 | 5.681 |
15 | 10 | 40 | 149.6 | 14.720 | 2.325 | 5.308 |
20 | 10 | 40 | 150.4 | 16.320 | 2.585 | 7.768 |
25 | 10 | 40 | 151.8 | 17.400 | 2.780 | 7.197 |
30 | 10 | 40 | 151.4 | 19.720 | 3.321 | 5.229 |
35 | 10 | 40 | 151.2 | 19.400 | 3.034 | 5.313 |
40 | 10 | 40 | 150.6 | 18.700 | 2.920 | 3.732 |
45 | 10 | 40 | 150.0 | 19.325 | 2.879 | 4.029 |
Conclusion
Conclusions from this research were as below:
- A minimum distance of threaded steel rod from the outer edge laminated bamboo before experiencing a decline of pull-out resistance was at 3d, with d was diameter threaded steel rod.
- The splitting failure on laminated bamboo occurred when the edge distance of threaded steel rod was less than 2d, whereas the distance of the threaded steel rod was more than or equal to 2d, the pulled failure of threaded steel rod from laminated bamboo occurred.
- The edge distance did not influence the magnitude of the slip modulus on the threaded steel rod glued-in laminated bamboo.
- The brittle failure occurred in a threaded steel rod glued-in laminated bamboo that experienced splitting or pulled failure.
Acknowledgement
This study was a part of fundamental research funded by The Ministry of Research, Technology and Higher Education of The Republic of Indonesia 2018.
Conflict of Interest
There’s no conflict of interest.
Author Details
Department of Civil Engineering, Faculty of Engineering, Universitas Negeri Malang, Malang, 65145, Indonesia
References
Rights and permissions
Open Access: This article is licensed under a Creative Commons Attribution 4.0 International License, which permits use, sharing, adaptation, distribution and reproduction in any medium or format, as long as you give appropriate credit to the original author(s) and the source, provide a link to the Creative Commons license, and indicate if changes were made. The images or other third-party material in this article are included in the article’s Creative Commons license, unless indicated otherwise in a credit line to the material. If material is not included in the article’s Creative Commons license and your intended use is not permitted by statutory regulation or exceeds the permitted use, you will need to obtain permission directly from the copyright holder. To view a copy of this license, visit http://creativecommons.org/licenses/by/4.0/
Cite this Article
DOI: http://doi.org/10.19026/rjaset.17.6027